Es geht um Ihren Erfolg. Mit uns.
Wir stehen für Sachverstand – zuverlässig, fokussiert und praxisorientiert.
Wir haben immer das gleiche Ziel: Zuverlässige, reibungslos laufende Planungen, Installationen und Abnahmen sowie Maschinen mit höchster Effizienz. Dafür spielt es keine Rolle, mit welchem Anlagenhersteller und welchem Betreiber wir arbeiten, denn unsere Handlungsbasis sind Fakten. Diese Fakten ermittelt niemand anderes im Markt seriöser und kompetenter als wir.
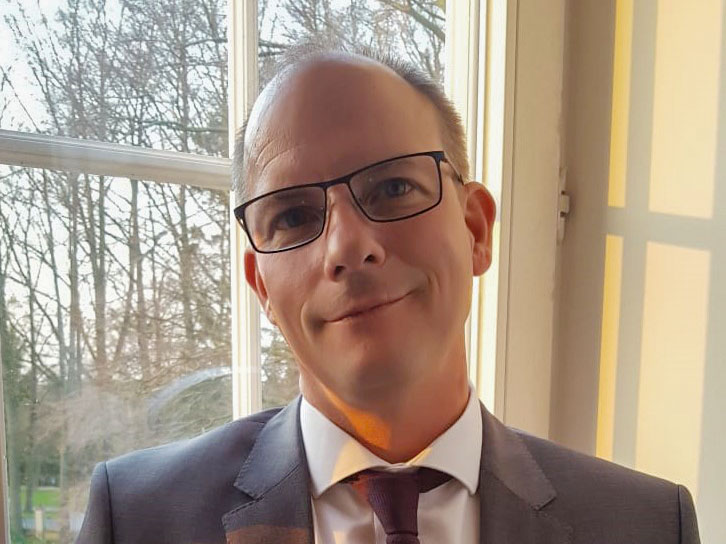
„Unser Ziel sind Ihre 100 %."
Dipl.-Ing. (FH) Gero Fiedler, Inhaber und Geschäftsführer
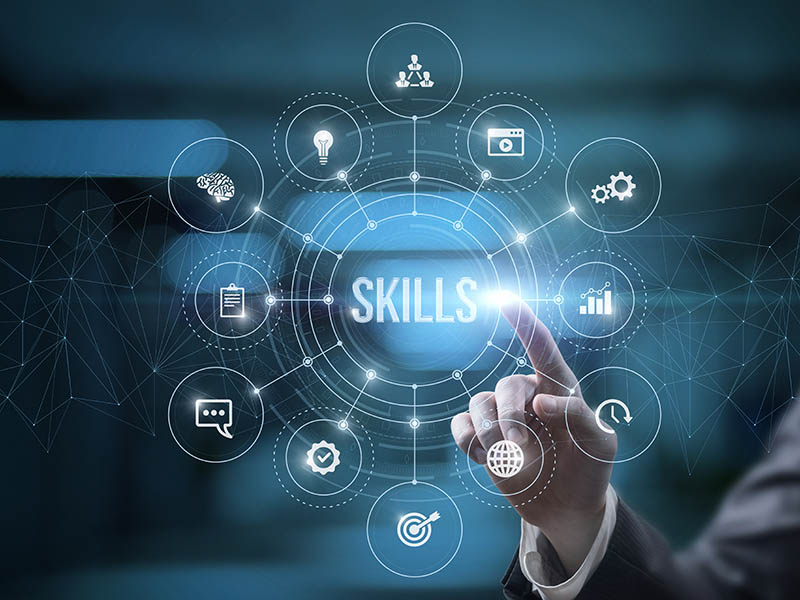
Erfahrung &
technischer Fortschritt
Unsere Erfahrung aus der Analyse, Leistungsabnahme und Optimierung von inzwischen weit über 500 verschiedenen Abfüll-Linien und Verpackungsmaschinen wird durch Begutachtung und Abnahmen der neuesten Maschinentechnik vor Ort ständig aktualisiert. In unseren weltweiten Einsätzen lernen wir auch Verfahrensweisen und Kennwerte kennen, die in Deutschland zwar sinnvoll, aber nicht üblich sind.
Ihr Weg zu dauerhaft hohem Wirkungsgrad
Die Kosten bei der Herstellung von Getränken und Lebensmitteln entfallen zu einem großen Teil auf das Abfüllen und Verpacken. Der Fokus einer kostenoptimierten Produktion sollte daher auch auf einer hohen Effizienz der Abfüll- und Verpackungslinien liegen. Hohe Wirkungsgrade von Neuanlagen können jedoch bei steigender Nutzungsdauer nicht ohne Überprüfung der Leistungsfähigkeit – in Verbindung mit korrigierenden Maßnahmen – aufrecht erhalten werden.
Die Geschichte der Linieneffizienz beginnt bereits bei den Verhandlungen zum Neukauf der Anlage. Hier werden u.a. Wirkungsgrade gefordert und vereinbart. Das Zustandekommen dieser entsteht aus dem Wunsch des Käufers, eine störungsfreie Anlage zu betreiben (100%) und dem Wissen um das wirtschaftlich mach- und gleichzeitig garantierbare durch den Maschinenhersteller (87-92%).
Es wird eine Leistung vereinbart, die über eine mehr oder weniger lange Zeitdauer durch Leistungsabnahme nachgewiesen werden muss. Häufig ist diese nicht repräsentativ für die Nutzungsweise der Anlage (z.B. 2 x 8h bei Anlagen, die im Dreischichtsystem betrieben werden).
Dieser Wirkungsgrad ist aber meist der im besten Fall (mit spezifikationskonformem Material, geschulten Mitarbeitern und von Profis eingestellten Maschinen) erzielbare Wirkungsgrad des maschinellen Teils einer Produktionslinie, also der Liefergrad nach DIN8782.
Gerne wird die Nomenklatur des Liefergrades durch den Kunden falsch interpretiert, da im Unternehmen auch ein so genannter Liefergrad ermittelt wird, der jedoch mit dem „Wirkungsgrad inkl. aller Störungen" nach DIN 8782 vergleichbar ist. Er liegt aufgrund des erweiterten Einflusses von Störquellen meist weit unter dem eingekauften Liefergrad. Allein durch diese Tatsache entsteht eine nicht unbedeutende Differenz zwischen dem Wirkungsgrad, der Grundlage für die Produktionsplanung ist, und der tatsächlich erzielbaren Ausbringungsleistung.
Nach bestandener Abnahme ist der vertraglich vereinbarte Wirkungsgrad nahezu belanglos.
Für den Betreiber ist dann die Summe aller Störquellen von Bedeutung.
Anfangs werden sich die reinen Maschinenstörungen auf geringem Niveau halten, jedoch die Fremdstörungen (aufgrund fehlenden Know-hows bzw. Erfahrung mit den neuen Aggregaten und möglicherweise angepasste Verhaltens- und Ablaufregeln) einen deutlich leistungsmindernden Einfluss bewirken.
Wie geht's weiter? Das Abfüllteam wird geübter, die Arbeitsabläufe greifen besser in einander, aber … die Linieneffizienz steigt nicht!
Die Gründe für das Ausbleiben der Effizienzsteigerung sind vielschichtig, da die Anlage mit den vollen Auswirkungen des betrieblichen Alltags konfrontiert wird.
Die automatische Linienüberwachung
In vielen Anlagen sind verschiedene Systeme der Linieneffizienz-Visualisierung eingebunden. Je nach Art und Aufwand der Installation geben diese Aufschluss über die Störanfälligkeit von Aggregaten und deren Auswirkung auf die Effizienz.
Leider sind diese Systeme immer nur so gut wie deren eingebundene Signale und die Auswertung durch Mitarbeiter. Die Schlussfolgerung und Umsetzung sind weiterhin erforderlich. Hierfür fehlt aber oft die Zeit. So wird bestenfalls nur bei deutlich störanfälligen Aggregaten ein Aktionsplan erstellt.
Aber wie aussagekräftig sind solche durch Überwachungssysteme ermittelten Peaks im Laufprofil der Anlage?
Wie bereits erwähnt, erfolgt die Datenerfassung durch Sensorik in Verbindung mit den Signalen der Einzelmaschinen. So kann mittlerweile eindeutig festgestellt werden, welches Aggregat etwa zu einem momentanen Füllerstillstand führt.
Schwachpunkte und Fehlinterpretationen durch diese Systeme sind jedoch vielschichtig, da hier nur Signale ausgewertet werden, die für sich selbst keine analytische Basis darstellen.
Die Fehlinterpretationsrate von automatisierten Linieneffizienzsystemen ist immens.
Selbst bei Weiterentwicklungen, die sich noch im wissenschaftlichen Status befinden, liegt diese Rate bei über 40 %.
Eine ständige Auswertung und Überprüfung der erfassten Daten durch betriebseigene Mitarbeiter ist zwingend erforderlich und führt zu einer nicht unerheblichen personellen Mehrbelastung.
Manuelle Leistungs- und Schwachstellenanalysen
Im Vergleich zu automatischen Linienanalyse-Systemen, die ihre Signale online und ständig erhalten, erfassen manuelle Analysen lediglich einen bestimmten Beobachtungszeitraum.
Dies ist jedoch für die Ermittlung von symptomatischen leistungsmindernden Faktoren (und nur diese stehen im Fokus einer Optimierung), deren Auftreten wiederkehrend erfolgt, von untergeordneter Bedeutung, wenn der Beobachtungszeitraum repräsentativ gewählt wird.
Bei der manuellen Linienanalyse werden sämtliche Störungsursachen lückenfrei aufgezeichnet und originär zugeordnet. Die zeitliche Verschiebung zwischen Ursache und Wirkung wird vollumfänglich berücksichtigt. Es erfolgt eine eindeutige Trennung zwischen „anlagenfremd" und „anlagebedingt" sowie die Berücksichtigung von weiteren negativen Einflussfaktoren und übergeordneten bzw. vor- und nachgeschalteten Systemen. Somit steht eine detaillierte Multimomentaufzeichnung mit Korrelationsanalyse (3D-Anlagenanalyse) zur Verfügung, anhand derer Optimierungspotenziale formuliert und ein zielgerichteter Maßnahmenkatalog erstellt werden kann. Das umfassende praktische Erfahrungspotenzial des Expertenteams aus einer Vielzahl unterschiedlicher Anlagen und Maschinen findet hierbei vollumfängliche Beachtung.
Für Ihre Planung: Im Allgemeinen nimmt eine manuelle Anlagenanalyse von Beginn einer 2- bis 5-tägigen Vororttätigkeit bis hin zur Vorlage des detaillierten Berichtes 7 bis 10 Werktage in Anspruch. Einzelleistungen wie ein Test vor einer Formatumstellung sind natürlich kurzfristiger realisierbar. Die Einbindung betriebseigener Mitarbeiter während dieser Zeit ist nicht erforderlich. Bestenfalls können während der Analyse bereits erste Optimierungsmaßnahmen in Zusammenarbeit mit der Instandhaltung vor Ort durchgeführt werden.
Da eine negative Beeinträchtigung der betrieblichen Abläufe durch unsere Beratung nicht stattfindet und die Mehrbelastung von Mitarbeitern und Management durch die autarke Analyseform sehr gering ist, können derartige Analysen auch während Saison- und Kampagnezeiten durchgeführt werden. Erkenntnisse und Ergebnisessenzen können direkt in die Investitionsplanung einfließen.
Die Kosten einer manuellen Analyse sind stark abhängig von der Beobachtungsdauer, den Gegebenheiten vor Ort sowie den unterschiedlichen Anbietern. Wenn Sie uns beauftragen ist jedoch davon auszugehen, dass durch die Verbesserung der Linieneffizienz und der möglichen Optimierung betrieblicher Abläufe und des geringen Einsatzes eigenen Personals bereits nach kurzer Zeit ein deutlicher Mehrwert resultiert.
FAZIT
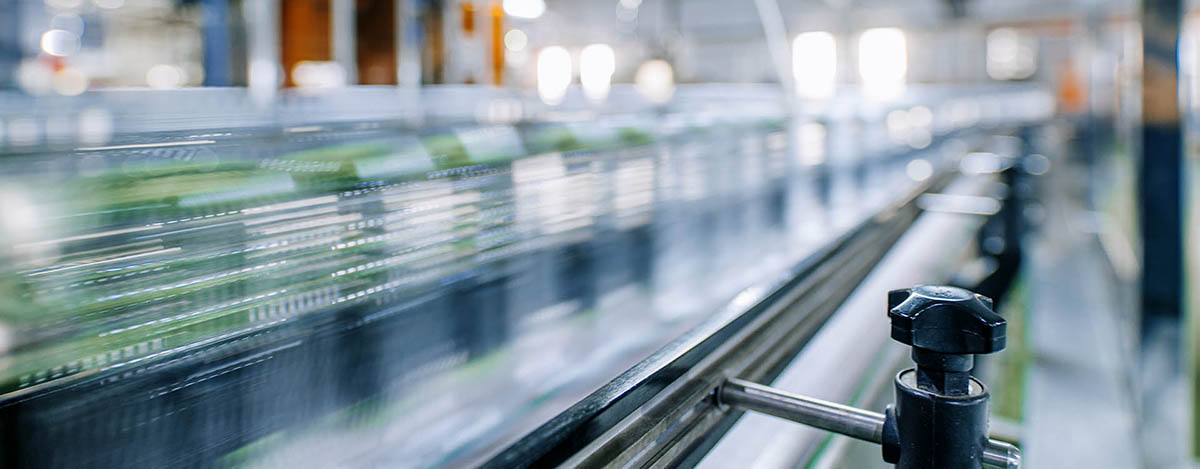