It's all about your success. With us.
We stand for expertise – reliable, focussed and practice-oriented.
We always have the same goal: reliable, smooth planning, installation and acceptance as well as machines with maximum efficiency. It doesn't matter which system manufacturer or operator we work with, because we base our actions on facts. No one else in the market is more reliable and competent than we are at determining these facts.
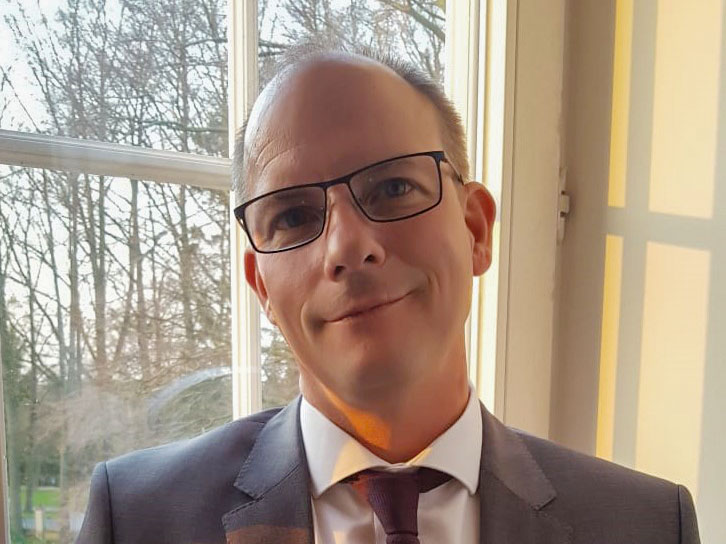
"Unquestionably independent, neutral and objective, even without an oath"
Dipl.-Ing. (FH) Gero Fiedler, Owner and Managing Director; Consultancy
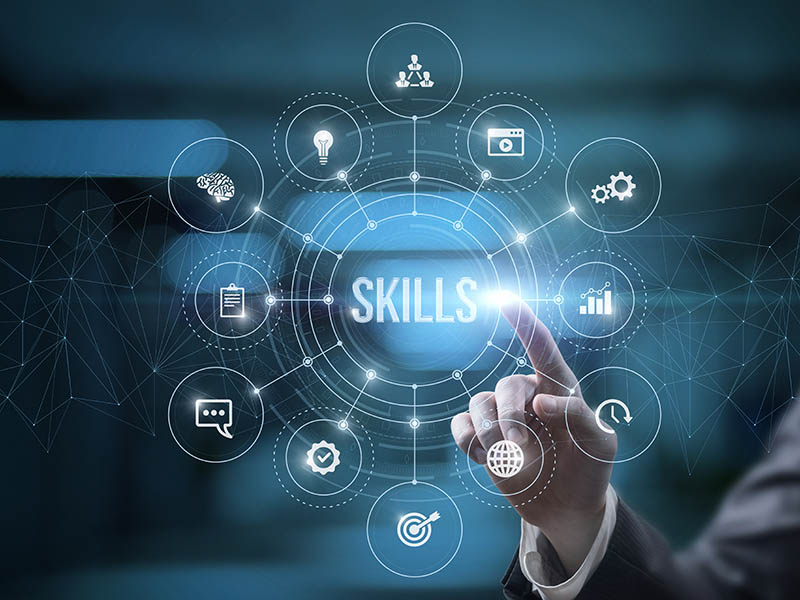
Experience &
technical progress
Our experience from analyses, approvals and optimisations of well over 500 different filling lines is constantly updated through approvals of the latest machine technology. During our worldwide assignments, we also familiarise ourselves with processes and parameters that are useful but not common in Germany.
Your path to permanently high efficiency
Filling and packaging account for a large proportion of the costs in the production of beverages and food. The focus of cost-optimised production should therefore also be on the high efficiency of the filling and packaging lines. However, the high efficiency of new systems cannot be maintained as their service life increases without checking their performance – in conjunction with corrective measures.
The story of line efficiency begins as early as the negotiations for the purchase of a new line. Among other things, efficiency levels are demanded and agreed here. These are the result of the buyer's desire to operate a trouble-free system (100%) and the machine manufacturer's knowledge of what is economically feasible and at the same time guaranteed (87-92%).
A performance is agreed that must be proven by acceptance over a more or less long period of time. This is often not representative of the way the system is utilised (e.g. 2 x 8 hours for systems that are operated in a three-shift system).
However, this efficiency is usually the efficiency of the machine part that can be achieved in the best case (with specification-compliant material, trained employees and machines set up by professionals), i.e. the degree of delivery according to DIN8782.
The nomenclature of the degree of delivery is often misinterpreted by the customer, as a so-called degree of delivery is also determined in the company, but this is comparable to the "degree of efficiency including all faults" according to DIN 8782. Due to the extended influence of interference sources, it is usually far below the purchased degree of delivery. This fact alone results in a not insignificant difference between the efficiency, which is the basis for production planning, and the actual achievable output.
Once acceptance has been passed, the contractually agreed efficiency is almost irrelevant.
For the operator, the sum of all sources of interference is then important.
Initially, the pure machine faults will remain at a low level, but the external faults (due to a lack of know-how or experience with the new units and possibly adapted behaviour and process rules) will have a significant performance-reducing effect.
What happens next? The filling team becomes more practised, the work processes interlock better, but … the line efficiency does not increase!
The reasons are complex, as the line is confronted with the full impact of day-to-day operations.
Automatic line monitoring
Various line efficiency visualisation systems are integrated in many plants. Depending on the type and complexity of the installation, these provide information about the susceptibility of units to faults and their impact on efficiency.
Unfortunately, these systems are only as good as their integrated signals and the evaluation by employees. Conclusions and implementation are still required. However, there is often not enough time for this. At best, an action plan is only drawn up for units that are clearly susceptible to faults.
But how meaningful are such peaks determined by monitoring systems in the running profile of the plant?
As already mentioned, data is recorded by sensors in conjunction with the signals from the individual machines. In this way, it is now possible to clearly determine which unit is causing a momentary filler standstill, for example.
However, the weak points and misinterpretations of these systems are complex, as they only analyse signals that do not in themselves represent an analytical basis.
The misinterpretation rate of automated line efficiency systems is immense.
Even with further developments that are still at the scientific stage, this rate is over 40 %.
Constant evaluation and checking of the recorded data by the company's own employees is absolutely essential and leads to a not inconsiderable additional workload.
Manual performance and weak point analyses
Compared to automatic line analysis systems, which receive their signals online and continuously, manual analyses only record a specific observation period.
However, this is of secondary importance for the determination of symptomatic performance-reducing factors (and only these are the focus of optimisation), the occurrence of which is recurring, if the observation period is selected to be representative.
In the manual line analysis, all causes of malfunctions are recorded without gaps and originally assigned. The time lag between cause and effect is fully taken into account. A clear distinction is made between "external to the system" and "caused by the system" and other negative influencing factors and higher-level or upstream and downstream systems are taken into account. This provides a detailed multi-moment recording with correlation analysis (3D system analysis), which can be used to formulate optimisation potential and create a targeted catalogue of measures. The extensive practical experience of the team of experts from a large number of different systems and machines is fully taken into account here.
In general, a manual system analysis takes 7 to 10 working days from the start of a 2 to 5-day on-site activity to the submission of the detailed report. It is not necessary to involve the company's own employees during this time. At best, initial optimisation measures can already be implemented on site during the analysis in cooperation with the maintenance department.
As our advice does not have a negative impact on operational processes and the additional workload for employees and management is very low due to the self-sufficient form of analysis, such analyses can also be carried out during seasonal and campaign periods. The results can be incorporated directly into investment planning.
The costs of a manual analysis are highly dependent on the observation period, the local conditions and the different providers. However, it can be assumed that the increase in line efficiency and the possible optimisation of operational processes and the low deployment of in-house personnel will result in significant added value after a short period of time.
CONCLUSION
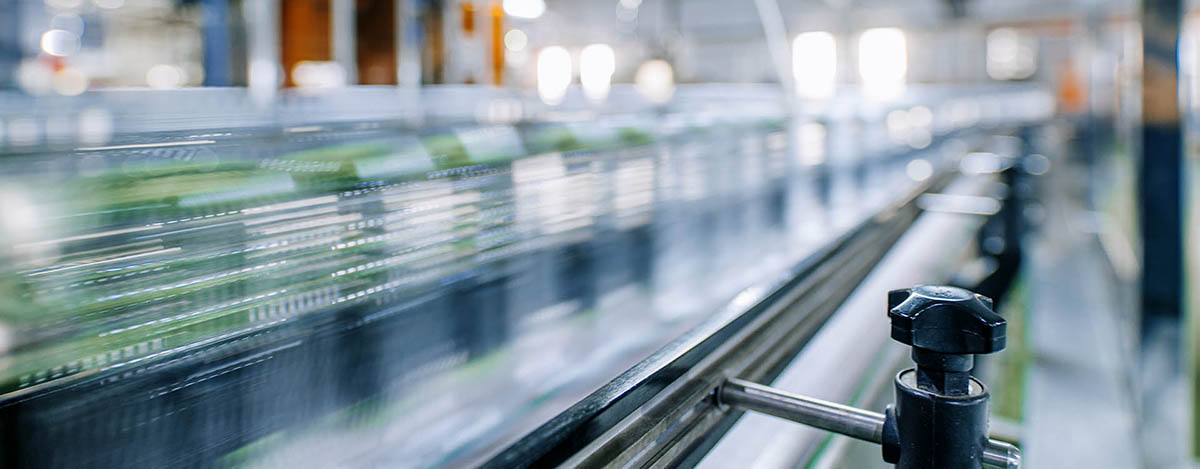